PPについて
PPはSAPの生産管理モジュールです。PPモジュールとは、生産管理モジュールを指します。
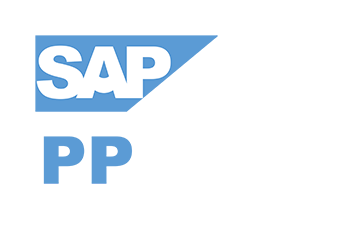
PP(Production Planning and Control:生産計画・管理)モジュールには「生産計画」と「製造実績」の2つの機能で構成され、これらには需要予測と販売予測に基づいた生産計画の機能、実際の生産の場面で発生する生産管理の機能があり、様々な生産形態に対応しています。
INDEX LINK
SAP PPモジュールとは?
PP(Production Planning and Control:生産計画・管理)モジュールには次の2つの機能で構成されています。
- 生産計画
- 製造実績
これらには需要予測と販売予測に基づいた生産計画の機能、実際の生産の場面で発生する生産管理の機能があり、様々な生産形態に対応しています。
生産計画
生産計画の業務は次の4つのプロセスで構成されています。
- 計画独立所要量登録または受注登録
- MPS・MRP(所要量計画)
- 能力計画
- 計画手配→製造指図・購買依頼へ変換
計画独立所要量登録または受注登録
計画独立所要量登録または受注登録では、生産計画のもととなる数量情報を登録します。「計画独立所要量登録または受注登録」にした理由は、メーカーによって生産形態が見込生産および受注生産の2タイプに分かれるためです。
見込生産
見込生産(MTS:Make to Stock )は小品種・大量生産を行う製品の製造の場合に使います。
需要予測や販売予測などをもとに、日用品などの製品や汎用品などをあらかじめ作っておき、定期的に売れる製品の欠品などを防ぎます。
量産することによりコストを下げることがメリットになりますが、過剰在庫が発生するリスクが起こります。
部品構成管理として部品表(BOM:Bill of Materials)やフォーミュラ(部品表と構成は同じであるが、副産物や連産品を扱うことができる)が使用され、原価の構成管理として原価計算表を使用します。
受注生産
受注生産(BTO:Bulid to Order)は、見込生産とは逆に多品種・少量生産を行う製品の製造の場合に使います。
受注の度に生産するため製品の在庫は基本的にありません。
さらに受注生産には、下記に記す3つの生産方式があります。
繰返受注生産方式(MTO:Make to Order)
あらかじめ製品の型などを作っておき、受注があると繰り返し生産を行います。
受注組立生産方式(ATO:Assemble to Order)
中間品までを見込生産で作っておき、受注があると組み立て生産を行います。
個別受注生産方式(ETO:Engineer to Order)
ビルや橋、道路など受注のたびに、設計なども行う受注生産です。個別生産の場合は、PPモジュールではなく、CS(プロジェクト管理)モジュールを使います。
MRP・MPS(所要量計画)
MRP・MPS(所要量計画)とは、下記のとおり受注数量もしくは計画独立所要量をもとに、製品または半製品をいくら生産しないといけないのか、材料をいくら発注しないといけないのかを計算します。
MRP(Material Requirement Planning)は、材料を発注するために算出します。
MPS(Master Production Schedule)は、製品・半製品をいくら作るかを算出します。
MRP・MPSは、受注数量もしくは計画独立所要量をもとに、現在の在庫数量、入庫予定数量、出庫予定数量、安全在庫数量から、これから発注する数量もしくは生産する数量を算出します。
入庫予定数量とは、すでに発注が済んでいるが、まだ仕入先から材料が届いてなく、これから入庫される予定の数量です。
出庫予定数量とは、生産計画をすでに立てていて、これから材料・半製品を使う予定の数量です。
安全在庫数量はとは、万が1のため最低限はこれだけの在庫をキープしておきたい数量のことです。
能力計画
能力計画は、MPSで算出した生産計画数量が作業時間内に製造できるかを計画します。
MPSはあくまでも何が、いつ、いくら必要なのかを計算するのみで、作業の負荷状況は考慮されていません。
そのためMPSの生産計画数量が、本当に生産可能なのか、作業能力に問題がないのかを計画するのが計画能力です。
SAP上で数か月先の計画独立所要量や受注が登録されている場合、数か月先の生産計画まで立案されます。
いつ能力負荷が高くなるのかを事前に把握し、あらかじめどのような手を打つのかを検討する事が生産計画担当者に求められます。
計画手配から製造指図・購買依頼への変換
MRP・MPSが実行されると計画手配という伝票が登録されます。計画手配とは、未だ指示(製造指図・購買依頼)が確定しておらず、あくまで予定というステータスです。
計画手配変換は、生産計画を実行し計画手配を確定ステータスにする業務です。MRP・MPSの実行、そして能力所要計画を終え、これで生産・発注に取り掛かっても問題ないと判断すれば、計画手配から製造指図・購買依頼依へ伝票を変換します。すなわち製品・半製品の場合は、計画手配から製造指図が登録され、材料の場合は、計画手配から購買依頼が登録されます。
整理すると、計画手配から製造指図・購買依頼へ変換するプロセスは、実務担当者が仕事を始める起点となります。
製造実績
製造実績は製品をいくら作ったか、製品を作るのに材料をいくら使ったか、製品を作るのにいくら作業時間がかかったかをシステムに計上します。
製造実績は製造指図という指示書をもとに作業します。
製造指図は生産計画をもとに登録されることもあれば、マニュアルで登録されることもあります。
どう登録するかはSAPを導入した会社の運用次第で、SAPで生産計画を立てていても急遽製造する必要になった場合は、マニュアルで製造指図を登録します。
仮にExcelやほかの生産管理システムで生産計画を立てている場合も、生産することが確定した製品だけマニュアルで製造指図を登録します。
製造実績では造指図をもとに、次の3つの情報を実績計上します。
- 構成品出庫(製品を作るのに材料をいくら使ったか)
- 生産品入庫(製品をいくら作ったか)
- 作業時間(製品を作るのにいくら作業時間がかかったか)
なお、上記3つの情報を計上する順番は問いません。
構成品出庫
構成品出庫では製品を作るのに材料をいくら使ったかを実績計上します。
製品Aを作る場合に、
- 金属:1枚
- ねじ:3個
- 箱:1個
という構成品出庫実績を計上します。
また、構成品出庫時には、
- 品目;製品A
- 数量:1個
- 保管場所:A倉庫
- ロット番号:0001
といった情報を入力します。
構成品出庫実績を計上すると、指定した品目、数量、保管場所、ロットの在庫が減ります。
ロットとは在庫のグループをいい、ロットには品質情報、製造日、有効期限日など品目マスタよりも細かい情報を持たせることができます。
生産品入庫
生産品入庫では製品をいくら作ったかを実績計上します。
例えば、
製品A:1個
という生産品入庫実績を計上します。
また、生産入庫時には、
品目:製品A
数量:1個
プラント:A工場
ロット番号:0001
といった情報を入力します。
生産品入庫実績を計上すると、指定した品目、数量、プラント、保管場所、ロットの在庫が増えます。
生産品に対しても、同じようにロット番号を付与します。
なぜロットの考え方が重要かと説明します。
車のエンジンを製造している会社で、生産ラインで10機ずつエンジンを作っています。
そのため、10個単位で同じロット(グルーピングという考え方になります)で生産品入庫計上します。
あってはならないのですが、エンジンを購入された得意先からトラブルのクレームがあったとします。調べてみると、同じロットで生産したほかのエンジンにも不具合がある可能性があることがわかりました。
そこで同じロットのほかの9機のエンジンもリコールという形で、ほかの得意先からもエンジンを回収します。
生産品入庫でロットの情報を入力することにより、生産品の細かな情報を管理できるようになります。
作業時間
作業時間では製品を作るのにいくら作業時間がかかったかを実績計上します。
例えば、
加工:4時間
組立:4時間
といったように、作業時間を計上した際に作業が完了したことも合わせて入力します。
この後、CO(管理会計)モジュールで加工費を計上します。
製造実績を計上するメリット
システムに製造実績を計上するメリットには、次の2つがあります。
- 在庫管理がリアルタイムに把握できる
- 製造原価を計算できる
生産入庫・構成品出庫をその都度、システムに入力することにより、在庫増減がリアルタイムで反映されます。在庫がリアルタイムに把握することにより、MRP・MPS(所要量計算)の実行で、正確な生産計画数量を算出することができ、生産担当者以外の人が生産の在庫状況を把握したりするのに役立ちます。
そのため、生産で出庫・入庫を行うたびに、実績計上できる運用検討を行うのが重要です。
製造原価計算では、「構成品出庫(材料費)+作業時間(加工費)」から、生産入庫(生産高)がいくらになったかを計算することができます。SAPではPP(生産計画・管理)とCO(管理会計)が1つのシステムでつながっていることにより、生産実績をもとに原価計算が自動でできます。
私が知っているメーカーでは、生産システムが単独で構築されていたり、オフラインで原価計算をしていたり、正しい製造原価情報を把握するのに時間がかかっています。SAPでは製造実績から原価計算までが1連の流れの中ででき、これがSAPを導入する大きなメリットの1つです。
PP(生産計画・管理)モジュールで使う組織
PPモジュールで使う2つの組織
PP(生産計画・管理)モジュールでは。次の二つの組織を使います。
- プラント(A工場、B工場、C工場など)
- 保管場所(A製造ライン、B倉庫、C冷蔵庫など)
プラント
プラントは、在庫情報(在庫数量や在庫金額)を管理する組織です。また、プラントは品目マスタ登録のキーにもなります。
在庫数量や在庫金額の管理粒度をどう設定するのかは、PPモジュールの視点でプラントをまとめるか、複数に分けるかなど品目マスタの設定をどうするかによります。
同じエンジンという品目でも、プラントごとに製造日数、MRPタイプ、ロットサイズ、入庫保管場所などの設定が可能です。
生産計画において、次のような項目を設定します。
- どのようなMRPタイプを使うのか
- 在庫をどの順番に消費させるのか(先入先出など)
- 生産するロットサイズ(単位)をいくらにするか
- 製造の準備時間・処理時間・移動時間はいくらかかるか
製造実績においては、次のような項目を設定します。
- 入庫するデフォルトの保管場所
- 構成品として出庫するデフォルトの保管場所
- バックフラッシュの有無
- 連産品とするか(1つの製造工程で、複数の品目ができるか)
例えばプラントを工場ごとに分ければ、生産計画のもととなる情報や、製造実績計上のもととなる情報の設定が工場ごとに設定できます。
工場ごとに生産計画の考えが異なる場合は。工場ごとにプラントを分けて設定し、それぞれ品目マスタの設定を行ったほうが有用です。
入庫・出庫のデフォルト保管場所は異なるので、製造指図登録時、製造実績計上時にマスタから保管場所が自動でセットされるので、運用が楽になります。
ただし工場ごとに分けたことで、工場ごとに品目マスタのメンテナンスを行う必要があるため、プラントを1つにまとめて会社全体で共通設定とするのも案になります。
保管場所
保管場所は、プラントよりも細かい単位で在庫数量管理ができる組織設定です。PPモジュールではどこからの在庫を構成品出庫するか、どこへ在庫を生産品入庫するか、という製造実績のところで保管場所を使用します。
例えばA製造ラインやB倉庫、C冷蔵庫といった在庫を置く場所を保管場所として設定します。どのような粒度で在庫数量を見られるような管理をしたいかが、保管場所設定粒度の検討ポイントになります。
PP(生産計画・管理)モジュールで使うマスタ
PPモジュールで使う5つのマスタ
PP(生産計画・管理)モジュールでは、次の5つのマスタを使います。
- 品目マスタ
- BOMマスタ
- 作業区マスタ
- 作業手順マスタ
- 製造バージョン
品目マスタは生産入庫する単位(製品A、半製品Bなど)でそれぞれ登録します。
BOM・作業手順はあらかじめ登録しておいた品目マスタを使用します。
作業区は作業手順登録時に紐づけ登録されます。
製造バージョンは、BOMを作業手順の紐づけ管理を行うマスタです。
品目マスタ
品目マスタには製造する品目を設定します。会社で言うと製品A、半製品Bなど生産して在庫管理する製品1つ1つを品目マスタとして登録していきます。
生産品目の場合、MRPビュー、作業計画ビューの設定が必要です。
設定では、
- どういう数量単位で生産するか(製造単位:個など)
- どういうロット数量単位で生産するか(10個ずつ)
- ロット管理するか
- ロットサイズをどうするのか
- どういうMRP計算ロジックを使うか
- バックフラッシュ(理論値払出)を有効にするか
- 生産したとき、デフォルトでどの保管場所に入庫するか
- 能力計算における準備時間・処理時間をどうするか
といった生産に必要な情報を設定します。
MRPビュー・作業計画ビューでは、1つの品目でもプラントごとに設定をしていきます。プラントごとに生産計画の立て方や管理方式が異なるので、1つの品目を複数のプラントで生産する場合は、それぞれのプラント単位で設定をしていく必要があります。
BOMマスタ
BOMとはBill of Materialの略で、部品表や配合表とも呼ばれます。生産に使用する材料・半製品の構成情報をマスタ登録します。
例えばエンジンを1機生産するときの構成として、金属、ねじ、箱がいくら必要なのかをBOMマスタに登録します。
また、箱を1個生産するときの構成として、厚紙、のり、ホッチキスの歯がいくら必要なのかをBOMマスタに登録します。
BOMマスタがどういうケースに使われるかというと、生産計画で5機エンジンが必要な場合、BOMマスタをもとに必要な金属、ねじ、箱の数量を算出します。製造実績ではエンジンを10機製造するのに、使用する構成品の数量が製造指図に登録されます。
作業区マスタ
作業区マスタには作業場所や製造機器の生産能力、作業時間を入力する項目を登録します。会社で言うと製造を行う組立ラインや包装ラインを作業区として登録します。
例えば組立ラインには、
生産能力:8時~22時(14時~15時は休憩)まで
個別能力数(作業者数):5人
などと登録することで1日13時間の生産能力があることを設定します。
作業手順マスタ
作業手順マスタには生産品を製造するのにどのような作業があるのか、それぞれの作業ごとにいくら時間がかかるのかを登録したマスタです。
例えばエンジンを1機作る作業手順は、
板金:1時間
組立:2時間
包装:1時間
といった工程にそれぞれ時間がかかるのかを算出する元情報になります。
製造実績ではエンジンを3機作るのに、
板金:3時間
組立:6時間
包装:3時間
上記のように時間をかけてくださいという製造指図に登録されます。
製造バージョンマスタ
製造バージョンマスタには、BOMマスタと作業手順マスタの組み合わせ情報を登録します。前提としてBOM,作業手順ともに、1つの生産品に対して複数個を登録します。
例えばBOMマスタでは、エンジンに使用する金属は通常1枚だが、精密なエンジンでは金属は2枚使用するというように、金属が1枚のBOMと2枚のBOMの2種類を登録することができます。
作業手順マスタでは製造ライン1を使用した場合は4時間で、製造ライン2を使用した場合には3時間というように、2種類の作業手順マスタを登録することができます。
製造バージョンではBOM、作業手順をどの組み合わせで使用するかを登録します。たとえBOM,作業手順が1種類ずつの場合でも、必ず製造バージョンで組み合わせを登録してあげる必要があります。
周辺システム:MES(製造実行システム)とは?
MES(Manufacturing Execution System:製造実行システム)とは製造工程を可視化し、作業者への指示や支援などを行うシステムです。
生産管理システムの一種ですが、各製造工程と連携して現場の状況を把握しやすい点がメリットです。
人や機械、設備といったリソースを最適化し、製造の属人化を解消するメリットが期待されます。
MESは生産ラインの各製造工程と連携して、原材料や部品の在庫・工程進捗などをリアルタイムに把握し、生産計画にもとづいた作業スケジュールの設計・管理者への指示出しなどが可能です。
人・機械・モノといった生産資源を最大限活用し、生産性向上を目的に導入されています。また現場作業を支援できるよう、タッチパネルやハンディターミナル・バーコードリーダー・ICタグなどの機器が用いられます。
生産管理フローの製造(実行)工程でSAPと連携
MESは製造業における生産管理フローのうち、製造(実行)工程に特化したシステムです。
そのため、広義には生産管理システムの一つといえます。
生産管理システムとは納期や生産数量といった生産に関わる情報を管理し、蓄積したデータから生産計画を立案するシステムです。
生産計画・工程管理・品質管理・原価管理などの製造プロセスに関わる範囲から、受注管理・在庫管理・購買管理など製造の前後のプロセスにまでおよびます。
すなわちSAPとMESとは業務範囲が違います。
MESは生産管理システムの工程管理機能に近い位置づけと理解するとよいでしょう。
MESの機能
MESは製造する製品によって必要な機能が異なるため、標準パッケージが存在しません。
企業や工場ごとに必要なデータや活用方法を定義したうえで、システムを構築します。
アメリカのMES推進団体であるMESAが定義した11の機能は以下のとおりです。
1.生産資源の配分と監視
生産資源を管理する機能です。対象は生産装置・工具・技能・資材・その他設備や文書など。資源の予約や割り振り機能が用意されている製品もあります。
2.仕様・文書管理
作業に必要となるドキュメントを管理します。作業指示書・レシピ(配合表)・図面・作業手順書・設計変更などの蓄積や編集機能を提供します。
3.設備の保守・保全管理
装置や工具の可用性を確保し、定期保全・予防保全のスケジュールを確定します。
4.製品品質管理
収集された測定データをリアルタイムで分析し、適正な品質管理を行います。
5.作業のスケジューリング
生産計画にもとづいて、詳細なスケジュールを立案します。勤務シフトにも対応します。
6.作業手配・製造指示
生産投入を管理する機能です。ジョブ・受注オーダ・バッチ・ロットなどの形で作業を開始します。工程内仕掛量の調整機能を提供する製品もあります。
7.作業者管理
作業者状況を監視する機能です。最適な作業割り当ての決定も可能です。
8.データ収集
各工程内の進捗状況をリアルタイムに収集します。自動収集はもちろん、スマートデバイスによる手動収集にも対応します。
9.プロセス管理
生産状況を監視し、作業者の意思決定を支援します。
10.製品の追跡と製品体系管理
仕掛品の場所と次の作業を把握する機能です。
11.実績分析
過去の履歴や計画と比較しながら生産の最新状況を報告します。
参考:History of the MESA Models – Manufacturing Enterprise Solutions Association|MESA International
MESの必要性
製造業は今や大量生産から少量多種生産の時代に移り変わり、従来の見込み生産ではなく適切な生産・在庫計画が求められます。
また、熟練技術者の経験や知識に頼って生産計画を立てていた企業が多いため、昨今の人材不足による属人化の解消が課題の企業も増えています。
MESを導入すると、工場間で連携して生産資源配分・人員配置などの細かな管理が可能です。
近年、国内では企業においてDX化が推進されています。
しかし、製造業においては完全に浸透しているとはいえません。
多様な働き方への順応・人手不足の解消・他国との競争力強化などの課題には、システム導入による企業・工場のDX化が欠かせません。
MESとSAPの関係性と違い
MESとSAPの違いはシステムの役割や対応する業務です。
SAPは生産管理フローにおいて、計画層の効率化を担います。
対して、MESは製造(実行)層を支援します。
どちらも限られた資源を最大限活用することが目的です。
互いに連携することで、生産と経営のさらなる効率化が実現します。
MESを導入するメリット
MESの導入により得られるメリットは以下のとおりです。
・業務効率化
作業進捗・在庫のリアルタイム把握、製造スケジュールの予測作業により、作業における無駄をなくせます。
・部門間の連携
設計・製造部門やサプライチェーンとの連携により、製造スケジュール・稼働状況の最適化が可能です。
・属人化の解消
各製造工程の実績を記録できるため、業務の標準化を叶えます。
・品質向上・不良品の発生防止
製品不備や不良品発生時の原因分析ができます。
周辺システム:生産計画スケジューラーとは?
生産スケジューラーとは人員や設備などのリソースと生産量とを照らし合わせ、必要なリソースを割り当てるシステムのことです。
適切な時間配分や在庫引当、作業員の割り振りなどが行えます。PPにも計画を立てる機能は含まれていますが、生産スケジューラーほど細やかな計画を作成できません。
生産計画における課題
かつて少品種大量生産が主流だった頃は、ベテラン作業員の経験による計画作成が一般的でした。
しかし現在は消費者ニーズの多様化にともない、短い納期で多品種少量生産が求められています。
そのため、急な差し込み案件や計画変更が発生しやすく、納期調整のために着手順の変更や残業シフトの変更など、きめ細やかなコントロールが必要になっています。
こうした外的な要因に加えて、製造業を支えてきたベテラン作業員の退職や人手不足といった内的要因もあり、時代に対応した変化が必要になっています。
属人的な生産スタイルから脱却し、限られた人材、設備の中で効率良く生産活動を行うために、生産スケジューラーが果たす役割は大きいです。
生産スケジューラー導入のメリット
生産スケジューラーはさまざまな工程を分単位、秒単位で並行してスケジュールを計画・立案できます。
これにより遅れている工程やボトルネックになっている工程がないか、いつどのタイミングでリソースを投下すべきか、などの判断が可能です。
その結果リードタイムの最適化や余剰在庫の圧縮、キャッシュフローの改善につながるというメリットがあります。
エクセルでの管理を行う際に見られる個人の主観によるスケジューリングから脱却することで、属人化の問題も解消されます。
生産活動を正確にシミュレートできる生産スケジューラーの導入によって、システムに編集を加えることで生産スケジューリングの進捗状況をデバイス上で把握することが可能となります。
つまり、生産現場の見える化によって致命的な遅れにつながる前に、改善策を講じることが可能になるというメリットがあります。